Ecarry è stato sviluppato nel 2018 ed è ora certificato secondo gli standard N1 e R100.
Rory Jackson ha testato su questo veicolo elettrico su misura per raccogliere rifiuti nelle strade strette delle città e dei centri storici
I pericoli dell’eccesso di CO2, NOX e altri gas serra provenienti dai rifiuti e dai camion merci nei centri urbani popolati rendono indispensabile l’elettrificazione di questi veicoli tradizionalmente con alimentazione a diesel. Ciò ha spinto aziende come Irizar (EME 10, estate 2021) e The Lion Electric Company (EME 5, inverno 2019) ad affrontare le sfide della progettazione di grandi veicoli elettrici per la raccolta dei rifiuti.
Tali veicoli sono adatti per percorrere strade larghe e spaziose, ma per molte strade urbane più strette, c’era necessità di una soluzione EV più compatta e agile. Sembra quindi naturale che un’azienda italiana metta a punto un veicolo commerciale leggero su misura per la raccolta dei rifiuti nelle zone storiche del paese.
Questo veicolo è ecarry, progettato e venduto da Green-G, una consociata di Goriziane E&C. Con sede a Villesse, nel nord-est Italia, è stata fondata originariamente per fornire servizi di manutenzione, riparazione e revisione (MRO) per veicoli militari, ma in seguito ha iniziato a fornire servizi tecnici e sviluppare macchinari specializzati per l’industria petrolifera e del gas.
Gli investimenti iniziali per Green-G sono stati effettuati nel 2018 dai membri di Goriziane, che hanno visto che le conoscenze e le competenze accumulate dall’azienda nella ricerca e sviluppo MRO potevano essere combinate per formare un nuovo OEM che sviluppa veicoli specializzati. Il suo primo veicolo elettrico, ecarry, è ora in produzione in serie e il suo sviluppo è stato guidato da Massimo Aretino, responsabile ricerca e sviluppo dell’azienda.
Filosofia del design
Dice: “Quando abbiamo iniziato lo sviluppo del primo concept, nella seconda metà del 2018, non c’era un quadro chiaro di come avrebbero dovuto essere i veicoli elettrici commerciali leggeri in futuro.
“Tesla stava costruendo veicoli elettrici su un sistema a 350 V, certamente, ma c’erano anche molti veicoli più piccoli che funzionavano a 96 V. Quindi fin dall’inizio abbiamo esaminato attentamente la tensione del nostro gruppo propulsore, perché tutto – ogni componente, ogni connessione, imballaggio e spaziatura derivano dal livello di tensione scelto per questo tipo di veicolo.
La ricerca e lo sviluppo del concept iniziale si sono quindi concentrati tanto sui componenti di tensione più disponibili quanto sulle dimensioni dell’EV, al fine di creare un veicolo commerciale leggero altamente specializzato per l’igiene urbana e la logistica. Pertanto Green-G voleva trovare il giusto equilibrio tra convenienza economica, efficienza e facilità d’uso.
“Abbiamo anche effettuato un ampio ma approssimativo studio iniziale con i tipi di aziende e autorità sanitarie che utilizzano quotidianamente veicoli come ecarry che ha determinato in gran parte le dimensioni del veicolo nonché la durata appropriata della sua giornata lavorativa”, Aretino dice.
Ecarry è quindi largo 1,59 m, lungo 5,64 me alto 1,93 m, con una carreggiata di circa 1,32 m e un passo di 2,5 m e, un’autonomia prevista di 8 ore prima di dover essere ricaricato. Nella sua forma base, ha una cabina a due posti e un pianale, che può essere dotato di un vano di carico aperto (con parafanghi laterali e portellone posteriore) o di un cassone ribaltabile posteriore.
Se lo si desidera, il dumper può essere azionato mediante una presa di forza elettrica. Un motore elettrico da 7,5 kW e un inverter azionano una pompa a ingranaggi elicoidali (scelta per la sua silenziosità rispetto alle opzioni alternative) che a sua volta alimenta l’idraulica necessaria per il dumper. In particolare, vengono spinti 20 litri/minuto di olio a 150 bar per generare la forza di sollevamento necessaria da un serbatoio da 35 litri.
“Il secondo problema principale era la batteria”, afferma Aretino. “Quando sai che il tuo veicolo elettrico deve rientrare in un certo insieme di dimensioni, le batterie si rivelano improvvisamente frustranti. Quindi, se scegli, ad esempio, la chimica o la tecnica di saldatura sbagliate per le tue celle, potresti presto scoprire che la quantità minima di energia di cui hai bisogno non si adatta al corpo del tuo veicolo elettrico.
“Per questo motivo, il secondo grande esercizio per il nostro processo di ricerca e sviluppo è stato uno studio di fattibilità della durata di circa 6 mesi sulle tecnologie relative alle capacità delle batterie. Ciò includeva simulazioni per ridurre il consumo energetico di ecarry in diversi ambienti virtuali per soddisfare il massimo accumulo di energia a bordo possibile, e quindi ottenere un tempo di funzionamento di 8 ore tra una ricarica e l’altra.
Fatto ciò, Green-G ha iniziato a cercare fornitori di batterie e propulsori per i primi prototipi. Lo sviluppo principale di ecarry si è concluso di fatto con la sua omologazione secondo gli standard di certificazione N1 e R100 nel novembre 2021 – Aretino osserva che questo sarebbe finito prima se non fosse stato per il Covid.
Mentre ecarry dovrebbe svolgere principalmente compiti di raccolta dei rifiuti, può essere configurato dagli allestitori per altri compiti, come il trasporto di unità di refrigerazione (a sinistra), spurgo (al centro) e piattaforme aeree (a destra)
L’azienda si è anche concentrata molto sull’ergonomia, adottando una linea simile a Workhorse, i cui furgoni postali elettrici sono stati costruiti per porre fine ai danni fisici e psicologici subiti dai corrieri statunitensi di furgoni postali con motore IC (vedi EME 10, estate 2021). Green-G ha quindi consultato i potenziali operatori di ecarry su ciò di cui avevano bisogno nella loro cabina ideale, il che significava creare un modello di cabina fisica in cui gli operatori potessero sedersi e suggerire modifiche.
Il risultato dell’adozione di questi suggerimenti diretti è che il pavimento della cabina si trova a soli 380 mm da terra, riducendo al minimo non solo lo sforzo necessario agli addetti alla sanificazione e alla logistica per entrare e uscire dall’ecarry, ma anche il rischio di incidenti e infortuni che derivano da altezze eccessive della cabina.
Il volume totale della cabina è di 3,5 m3, per consentire comfort e facilità di pulizia e per prevenire crampi e lesioni da sforzo ripetitivo comuni agli utenti di piccoli veicoli commerciali. Inoltre, il parabrezza panoramico e gli specchietti laterali (regolabili elettricamente) massimizzano la visibilità dei pedoni tra cui il veicolo elettrico potrebbe dover guidare.
La resistenza agli sbalzi climatici stagionali del Mediterraneo è garantita da quattro prese d’aria per l’aria condizionata e un set di resistenze ad alta densità per lo sbrinamento elettrico del parabrezza, con un display grafico LCD per la visualizzazione di tutti i parametri di salute e prestazioni necessari della batteria e del gruppo propulsore secondo necessità . Un bus a 12 V dalla batteria (tramite un convertitore CC-CC dietro la cabina) fornisce tutti i requisiti di alimentazione per i sistemi della cabina.
“La cabina ha una forma insolita per un veicolo leggero per la raccolta dei rifiuti, ma il feedback dei nostri utenti è molto positivo, anche per quanto riguarda il modo in cui abbiamo progettato la trasmissione e la struttura del veicolo”, aggiunge Aretino.
Costruzione
Green-G in genere costruisce internamente il telaio di ecarry prima di inviare l’assemblaggio della carrozzeria ad aziende specializzate. Il telaio include anche tutti i componenti del gruppo propulsore montati dietro l’abitacolo, sebbene Green-G dia libertà agli assemblatori di carrozzerie di spostare i componenti se necessario, per facilitare la manutenzione o l’installazione del pannello della carrozzeria.
“Installiamo i nostri pacchi batteria da 400 V, un caricabatterie di bordo [OBC] da 7,2 kW, un motore e un inverter in una configurazione a trazione posteriore, nonché i sistemi della cabina come il display, i pedali, il volante e così via, dice Aretino. “Ma lasciamo uno spazio vuoto dentro e intorno al cruscotto nel caso in cui il carrozziere desideri integrare componenti come display o pulsanti aggiuntivi per le apparecchiature degli utenti finali che hanno installato”.
La struttura su cui sono montati è stata ottimizzata per bilanciare peso e robustezza. Come osserva Aretino, c’è un limite alla robustezza che un progetto di camion per la logistica e rifiuti leggeri può sacrificare per realizzare un veicolo elettrico più leggero ed efficiente dal punto di vista energetico. Secondo una ricerca di mercato, l’ecarry è progettato per essere abbastanza robusto da trasportare fino a 295 kg di batterie e 1700 kg di rifiuti o merci sul telaio.
“Ciò ha portato a scelte come le sospensioni a balestra anteriori e posteriori”, afferma. “Non potevamo applicare un normale sistema di sospensione, perché questi tipi di veicoli trascorrono la maggior parte del loro tempo più a pieno carico che a vuoto.
“Per quanto riguarda l’assale, ne abbiamo scelto uno fisso davanti e dietro, per garantire che a pieno carico non si rischiasse di danneggiare nessuno dei componenti della catena cinematica. Ciò riduce anche il numero di componenti e quindi i costi di manutenzione per ecarry rispetto ad alcune delle altre scelte di assali per cui avremmo potuto optare. I requisiti di manutenzione per i veicoli dei rifiuti leggeri sono normalmente enormi, quindi l’utilizzo di componenti meno numerosi ma più resistenti era davvero importante.
Le versioni future di ecarry potrebbero essere costruite con materiali compositi per risparmiare peso, ma al momento la struttura è costituita in gran parte da parti in acciaio standard del settore per ottimizzare la resistenza rispetto al costo e per garantire la disponibilità dei componenti strutturali.
Batteria
Dopo un’approfondita ricerca su quali sistemi di batterie fossero disponibili che potessero essere omologati allo standard di certificazione R100, Green-G ha optato per i pacchi prodotti da Webasto, così come la sua certificazione BMS – R100 richiede che i pacchi batteria conformi vengano forniti con i propri BMS interni.
È possibile installare uno o due pacchi batteria, ciascuno contenente 35 kWh e del peso di 147,5 kg, con un’autonomia fino a 250 km tra una ricarica e l’altra (testato secondo gli standard WLTP) se sono installati due pacchi.
“Parte di quella ricerca includeva l’esame delle celle al nichel manganese cobalto (NMC) e al litio ferro fosfato (LFP), inclusa la realizzazione dei nostri prototipi con celle LFP per saperne di più sulla progettazione della batteria e del BMS”, afferma Aretino. “Nel 2018, tuttavia, le celle LFP erano circa il 30% più grandi e più pesanti delle celle NMC di capacità energetica equivalente, quindi alla fine abbiamo optato per le NMC.
“Sappiamo che NMC e LFP stanno arrivando alla pari in termini di energia specifica e densità di energia, quindi siamo aperti allo scambio di tecnologie cellulari in futuro se LFP consentirà ai nostri veicoli elettrici di trasportare più carico utile durante la loro giornata lavorativa”.
Mentre per ecarry vengono utilizzati l’hardware BMS standard e i bus di segnale di Webasto, Green-G ha scritto internamente i propri algoritmi BMS per consentire la gestione in parallelo dei due pacchi batteria (quando ne sono installati due) da un singolo BMS controller, in modo che se una batteria e/o un BMS dovesse essere compromessa, i restanti pacchi possono ancora essere monitorati e azionati dal restante BMS.
“Ad essere onesti, non abbiamo ancora avuto la necessità di utilizzarlo: abbiamo riscontrato che i nostri pacchi batteria sono di altissima qualità, quindi non abbiamo ancora avuto guasti”, osserva Aretino. “Uno dei nostri ecarry è stato utilizzato per più di 10.000 km, in ambienti sia molto caldi che molto freddi, e in diverse prove lo abbiamo utilizzato senza attivare il circuito di raffreddamento a liquido nelle batterie. Ad oggi, quel veicolo non ha avuto problemi con le sue batterie.
“Inoltre, Webasto installa la crittografia sulle sue batterie, quindi nella remota possibilità che qualcuno tenti un furto, i pacchetti non possono essere utilizzati da nessun altro in quanto è un sistema di comunicazione chiuso.”
Sistemi di azionamento
L’invertitore e il motore sono montati l’uno vicino all’altro sull’assale posteriore, come ci si aspetterebbe in un veicolo a trazione posteriore e propulsore per impieghi gravosi, con una trasmissione a velocità singola e un rapporto di riduzione di 12,55:1. Ciò, combinato con la programmazione della ECU dell’inverter, limita ecarry a una velocità massima sicura di 80 km/h.
Il motore è una macchina a magneti permanenti che funziona con un ingresso nominale di 350 V, che eroga fino a 90 kW alla potenza di picco, fino a 380 Nm di coppia e 60 kW di potenza durante il normale funzionamento. L’inverter è progettato per un’alimentazione di picco di 400 V e corrisponde alla potenza nominale del motore a 60 kW.
“Abbiamo anche scelto un motore costruito attorno a uno statore a forcina, poiché riteniamo che massimizzerà la densità di coppia”, afferma Aretino. “Tutte le curve di potenza, coppia e velocità sono impostate internamente tramite i nostri algoritmi di controllo e abbiamo investito molto tempo e denaro per impostare correttamente tali dinamiche prestazionali.
“Fare questo è stato importante, perché il peso e l’inerzia di ecarry cambiano enormemente tra l’essere vuoto e completamente carico, quindi abbiamo dovuto costruire la nostra strategia di controllo per il bene di caratteristiche come la rigenerazione stabile e il comfort del conducente.
“I nostri algoritmi per l’inverter e il motore garantiscono un movimento fluido con la stessa accelerazione e decelerazione indipendentemente dalla velocità, dal carico utile e dall’inclinazione o dalla discesa su cui sta guidando l’utente finale.”
Aretino aggiunge che la frenata rigenerativa consente di generare fino a 25-26 kW di potenza attraverso il gruppo propulsore di ecarry (tipicamente sostenuto quando si è in discesa). L’algoritmo di controllo del motore include anche la funzionalità di controllo vettoriale per il blocco dell’angolo del rotore, abilitando funzioni come la tenuta in salita insieme alla precisione desiderata della coppia e del numero di giri per una guida fluida e transitori.
Sistema di Ricarica
Oltre a questo recupero dell’energia della batteria, Green-G mira a fornire quante più opzioni di ricarica possibili, per garantire che le batterie di ecarry possano essere ricaricate efficacemente da qualsiasi fonte CA, poiché i punti di ricarica disponibili sono ancora pochi e distanti tra loro in molti luoghi.
L’OBC monofase da 7,2 kW di serie è stato scelto per adattarsi alle diffuse prese da 32 A disponibili nei centri industriali e commerciali italiani. Praticamente qualsiasi connessione industriale, fino agli input di potenza più bassi delle abitazioni, è compatibile con ecarry.
“Per ogni livello di ricarica e protocollo esistente, prendiamo le specifiche e quindi sviluppiamo internamente il protocollo conforme”, afferma Aretino. “Lo facciamo perché vogliamo comprendere ogni aspetto di come la ricarica viene gestita attraverso il software di controllo, per garantire che l’energia sia sempre richiesta dalle stazioni di ricarica in modo chiaro e sicuro e che si traduca nelle migliori e più efficienti prestazioni di ricarica possibili. ”
Aggiunge che ciò è reso possibile anche dalla fornitura di cavi di ricarica Mennekes, adattatori da 32 A trifase a monofase e una gamma di altri accessori di ricarica.
“Adesso abbiamo anche clienti che richiedono una ricarica CC rapida. Abbiamo sviluppato tutto il necessario per la ricarica rapida di tipo CHAdeMO, e presto saremo in grado di installare i sistemi CCS anche sull’ecarry, su richiesta”, commenta Aretino.
Gestione termica
Tutti i componenti elettrici ed elettronici dell’ecarry sono gestiti termicamente utilizzando il raffreddamento a liquido, principalmente perché le sue operazioni di raccolta dei rifiuti richiederanno basse velocità e coppie elevate. Ciò non solo significa che viene generato un flusso d’aria insufficiente per il raffreddamento di qualsiasi componente, ma viene generato più calore e stress rispetto al tipico EV a causa della coppia più elevata e quindi della densità di corrente.
“Certo, è un po’ complicato gestire tutto con precisione, poiché il calore prodotto dal gruppo propulsore oscillerà durante le operazioni, e quindi può raggiungere il caricabatterie quando sei fermo e stai ricaricando”, osserva Aretino.
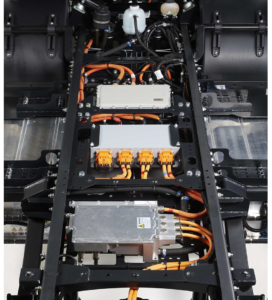
“Inoltre, ci sono notevoli oscillazioni delle temperature ambientali tra il nord e il sud dell’Italia che devono essere compensate. Quindi abbiamo fatto molti test per ottimizzare la nostra gestione del refrigerante, tra cui sostare ecarry al sole nei giorni più caldi dell’anno con una carica ad alta potenza per sottoporre a stress test l’OBC e fare ripetuti stop-and-start drive up e giù per le colline per vedere quali problemi termici incontrerebbe il propulsore.
Un circuito liquido corre tra le batterie e la cabina, dati i requisiti di temperatura simili tra gli esseri umani e le celle della batteria. Un altro corre tra l’inverter e l’OBC, poiché il gruppo propulsore generalmente si alterna tra i due, ed entrambi subiscono picchi simili durante l’uso, creando requisiti simili negli algoritmi di controllo e pressione del liquido.
Mentre l’acqua viene utilizzata come mezzo di raffreddamento in questi, un sistema di raffreddamento dell’olio impedisce il surriscaldamento del motore; L’Aretino osserva che l’utilizzo del petrolio consente l’utilizzo di un motore più piccolo con una densità di potenza maggiore rispetto a quando l’azienda avesse scelto l’acqua.
“L’utilizzo di un piccolo motore elettrico è importante per noi”, afferma. “Come veicolo commerciale leggero, non possiamo rendere ecarry troppo alto, lungo o largo per ospitare un motore sovradimensionato.”
Articolo Originale: https://www.emobility-engineering.com/green-g-ecarry/