The ecarry began development in 2018 and is now certified to N1 and R100 standards
The dangers of excess CO2, NOX and other greenhouse gases from refuse and freight trucks in populated urban centres makes it imperative to electrify such traditionally diesel-hungry vehicles. This has spurred companies such as Irizar (EME 10, Summer 2021) and The Lion Electric Company (EME 5, Winter 2019) to tackle the challenges of engineering large waste collection EVs to provide cleaner refuse collection services.
Such vehicles are well-suited to wherever roads are wide and spacious, but for many older and hence narrower streets in urban areas around the world, a more compact and nimble EV solution makes far more sense. It therefore seems natural that an Italian company would devise a light commercial truck that is tailored to duties such as refuse collection from the country’s countless historical urban beauty spots.
That truck is the ecarry, designed and sold by Green-G, a subsidiary of Goriziane E&C. Based in Villesse in north-east Italy it was founded originally to provide maintenance, repair and overhaul (MRO) services for military vehicles, but later started providing technical services and developing specialised machinery for the oil & gas industry.
Initial investments for Green-G were made in 2018 by members of Goriziane, who saw that the company’s accumulated knowledge and skills in MRO r&d could be combined to form a new OEM developing specialised vehicles. Its first EV, the ecarry, is now in series production, and its development has been spearheaded by Massimo Aretino, the company’s r&d manager.
Design philosophy
He says, “At the time we started the first concept development, in the second half of 2018, there was no clear picture of what light commercial EVs were supposed to look like in the future.
“Tesla was constructing EVs on a 350 V system, certainly, but there were also a lot of smaller vehicles running on 96 V. So from the outset we looked intensively at the voltage of our powertrain, because everything – every component, every connection, packaging and spacing – follows from the voltage level you pick for this kind of vehicle.”
Early concept r&d therefore focused as much on the most available voltage components as on the dimensions of the EV, in order to create a highly specialised light commercial vehicle for urban sanitation and logistics. Thus Green-G wanted to strike the right balance between cost-effectiveness, efficiency and user-friendliness.
“We also carried out a large but rough initial study with the kinds of sanitation companies and authorities who use vehicles like the ecarry every day, and that largely determined the dimensions of the vehicle as well as the appropriate length of its working day,” Aretino says.
The ecarry is therefore 1.59 m wide, 5.64 m long and 1.93 m tall, with about a 1.32 m track and a 2.5 m wheelbase, and an 8 hour expected operating time before needing to recharge. In its basic form, it has a two-seater cabin in front and a bare flatbed behind, which can be fitted with an open cargo bay (with side fenders and a tailgate) or a rear-tip dumper.
The dumper can be actuated if desired using an electric power take-off. A 7.5 kW electric motor and inverter drive a helical gear pump (chosen for its quietness relative to alternative options) that in turn powers the necessary hydraulics for the dumper. More specifically, 20 litres/minute of oil is propelled at 150 bar to generate the required lifting force from a 35 litre tank.
“The second major issue was the battery,” Aretino says. “When you know your EV needs to fit within a certain set of dimensions, the batteries suddenly come across as being frustratingly large. So if you choose, say, the wrong chemistry or welding technique for your cells going in, you could soon discover that the amount of energy you need as a minimum just doesn’t fit on your EV’s body.
“For that reason, the second big exercise for our r&d process was a feasibility study lasting 6 months or so of technologies relating to battery capacities. That included simulations of tightening the energy consumption of the ecarry across different virtual environments to meet the highest feasible onboard energy storage, and so end up with the 8 hour operating time between charges.”
Once that had been done, Green-G began searching for battery and powertrain suppliers for the first prototypes. Core development of the ecarry effectively concluded with its homologation according to the N1 and R100 certification standards in November 2021 – Aretino notes that this would have finished sooner if not for Covid.
While the ecarry is expected to take on largely refuse collection duties, it can be configured by body builders for other tasks, such as carrying refigeration units (left), pump tanks (centre) and aerial platforms such as cherry pickers (right)
The company also concentrated heavily on ergonomics, taking a similar line to Workhorse, whose EV postal vans were built around ending the physical and psychological damage suffered by US delivery drivers of IC-engined postal vans (see EME 10, Summer 2021). Green-G therefore consulted potential operators of the ecarry as to what they needed in their ideal cabin, which meant creating a physical cabin mock-up the operators could sit in, judge, and suggest modifications for.
The result of adopting these direct suggestions is that the cabin floor sits only 380 mm off the ground, minimising not just the effort needed for sanitation and logistics labourers to get in and out of the ecarry, but also the risk of accidents and injuries that stem from excessive cabin heights.
The cabin’s total volume is 3.5 m3, to enable comfort and easy cleaning, and to prevent cramping and repetitive strain injuries common to users of small commercial vehicles. Also, the panoramic windshield and (electrically adjustable) side mirrors maximise visibility of the pedestrians that the EV might need to drive among.
Resilience against the seasonal climate swings of the Mediterranean is provided through four air conditioning vents and a set of high-density resistors for electric windshield defrosting, with an LCD graphic display for viewing all the necessary health and performance parameters of the battery and powertrain as needed. A 12 V bus from the battery (via a DC-DC converter behind the cabin) supplies all the power requirements for the cabin’s systems.
“The cabin has an unusual shape for a light garbage collection vehicle, but the feedback from our users is very positive – including in how we’ve designed the drivetrain and the vehicle’s structure,” Aretino adds.
Construction
Green-G typically builds the chassis of the ecarry in-house before sending the body’s assembly to specialist companies. The chassis also includes all the powertrain components mounted behind the cabin, although Green-G gives freedom to the body assemblers to move components around if needed, for ease of maintenance or body panel installation.
“We install our 400 V battery packs, a 7.2 kW onboard charger [OBC], a motor and inverter in a rear-wheel-drive configuration, as well as the cabin systems such as the display, pedals, steering wheel and so on,” Aretino says. “But we leave some empty space in and around the dash in case the body assembler wants to integrate components such as extra displays or buttons for end-users’ equipment they’ve installed.”
The structure about which they are mounted has been optimised for balancing weight and toughness. As Aretino notes, there is a limit to how much toughness a light refuse and logistics truck design can sacrifice in order to make a lighter and more energy-efficient EV. As per market research, the ecarry is designed to be strong enough to carry up to 295 kg of batteries and 1700 kg of waste or cargo on its frame.
“That led to choices such as leaf spring suspension on the front and rear,” he says. “We couldn’t apply a normal suspension system, because these kinds of vehicles spend most of their time closer to full load than empty.
“As for the axle, we went with one that is fixed on the front and rear, to guarantee that full loading wouldn’t risk damaging any of the powertrain components. That also reduces the number of components and hence the maintenance burden for the ecarry, compared with some of the other axle choices we could have gone down. Maintenance requirements for light refuse trucks are normally huge, so using fewer but tougher components was really important.”
Future versions of the ecarry might be built with composite materials to save weight, but at present the structure is largely industry-standard steel parts for the sake of optimising strength versus cost, and to guarantee the availability of structural components.
Battery
After considerable research into what battery systems were available that could be homologated to the R100 certification standard, Green-G went with packs made by Webasto, as well as its BMS – R100 certification requires that compliant battery packs come with their own internal BMSs.
Either one or two battery packs can be installed, each containing 35 kWh and weighing 147.5 kg, with up to 250 km of range between charges being possible (tested to WLTP standards) if two packs are installed.
“Part of that research included looking into both nickel manganese cobalt (NMC) and lithium iron phosphate (LFP) cells, including making our own prototype packs with LFP cells to learn more about battery and BMS design,” Aretino says. “In 2018 though, LFP cells were around 30% bigger and heavier than NMC cells of equivalent energy capacity, so we went with NMC in the end.
“We know NMC and LFP are coming to a par in terms of specific energy and energy density though, so we’re open to swapping cell technologies in the future if LFP enables our EVs to carry more payload weight during their working day.”
While the standard-issue BMS hardware and signal buses from Webasto are used in the ecarry, Green-G wrote its own BMS algorithms in-house to enable the two battery packs (when two are installed) to be managed in parallel from a single BMS controller, so that if one battery and/or one BMS should be compromised, the remaining pack(s) can still be monitored and operated from the remaining BMS.
“To be honest, we’ve not had to use that yet – we’ve found our battery packs to be of very high quality, so we’ve had no failures yet,” Aretino notes. “One of our ecarrys has been used for more than 10,000 km now, across very hot as well as very cold environments, and in several trials we ran it without activating the liquid-cooling circuit in the batteries . To date, that vehicle has had no problems with its batteries.
“Also, Webasto installs cryptography on its batteries, so on the off-chance someone tries to steal the packs, they can’t be used by anyone else, it’s a closed comms system.”
Drive systems
The inverter and motor are mounted closely together on the rear axle, as would be expected in a heavy-duty rear-drive vehicle and powertrain, with a single-speed transmission and a 12.55:1 reduction ratio. That, combined with the programming of the inverter’s ECU, limits the ecarry to a safe top speed of 80 kph.
The motor is a permanent magnet machine operating on a nominal 350 V input, which outputs up to 90 kW at peak power, up to 380 Nm of torque and 60 kW of power during normal operation. The inverter is designed for a peak power supply of 400 V and matches the nominal rating of the motor at 60 kW.
“We’ve also chosen a motor built around a hairpin stator, as we feel that will maximise the torque density,” Aretino says. “All the curves for power, torque and speed are set in-house through our control algorithms, and we invested a lot of time and money into setting those performance dynamics correctly.
“Doing that was important, because the ecarry’s weight and inertia change hugely between being empty and fully loaded, so we had to build our own control strategy for the sake of features such as stable regeneration and driver comfort – sanitation workers hate feeling a ‘punch’ in the stomach when releasing the brake pedal.
“Our algorithms for the inverter and motor guarantee smooth motion with the same acceleration and deceleration regardless of the speed, payload, and incline or decline the end-user is driving on.”
Aretino adds that the regenerative braking enables up to 25-26 kW of power to be generated through the ecarry’s powertrain (typically sustained when on a downward slope). The motor control algorithm also includes vector control functionality for locking in the rotor angle, enabling functions such as hill-holding along with the desired precision of torque and rpm targeting for smooth driving and transients.
Charging strategy
In addition to this recouping of battery energy, Green-G aims to provide as many charging options as possible, to ensure the ecarry’s batteries can be replenished from effectively any AC source, as available charge points are still few and far between in many places.
The standard issue 7.2 kW monophase OBC was chosen to suit the widespread 32 A outlets available across Italy’s industrial and commercial centres. Practically any industrial connection, down to the very lowest power inputs from homes, is compatible with the ecarry.
“For every charging level and protocol there is, we take the specification and then develop the compliant protocol in-house,” Aretino says. “We do that because we want to understand every aspect of how charging is managed through the control software, to ensure power is always requested from the charging stations in a clear and safe manner, and results in the best, most efficient recharging performance possible.”
He adds that this is also enabled through the provision of Mennekes charging cables, three-phase to single-phase 32 A adapters, and a range of other charging accessories.
“We also have clients asking for fast DC-charging as well now. We’ve developed everything needed for CHAdeMO-type fast charging, and we’ll soon be able to install CCS systems on the ecarry too, upon request,” Aretino comments.
Thermal management
All electric and electronic components on the ecarry are thermally managed using liquid cooling, principally because its waste collection operations will require slow speeds and high torques. Not only does that mean insufficient airflow is generated for cooling any components, but more heat and stress is generated than the typical EV because of the higher torque and hence current density.
“Of course, it’s a little tricky to manage everything precisely, as the heat produced by the powertrain will oscillate during operations, and then it can spike at the charger when you’re sitting still and recharging,” Aretino notes.
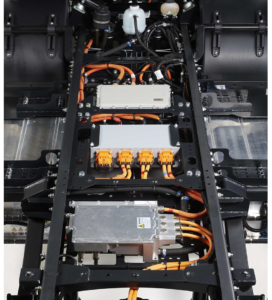
“On top of that, there are considerable swings in ambient temperatures between the north and south of Italy that need to be compensated for. So we did a lot of testing to optimise our coolant management, including sitting the ecarry in the sun on the hottest days of the year with a high-power charge to stress-test the OBC, and doing repeated stop-and-start drives up and down hills to see what thermal problems the powertrain would encounter.”
One liquid circuit runs between the batteries and cabin, given the similar temperature requirements between humans and battery cells. Another runs between the inverter and OBC, as the powertrain generally alternates between the two, and both of them experience similar spikes during usage, creating similar requirements in the liquid’s pressure and control algorithms.
While water is used as the cooling medium in these, an oil cooling system keeps the motor from overheating; Aretino remarks that using oil enables the use of a smaller motor with a higher power density than if the company had chosen water.
“Using a small e-motor is important for us,” he says. “As a light commercial vehicle, we can’t make the ecarry too tall, long or wide to accommodate an oversized motor.”
Articolo Originale: https://www.emobility-engineering.com/green-g-ecarry/